Processo di costruzione di un cerchio in lega
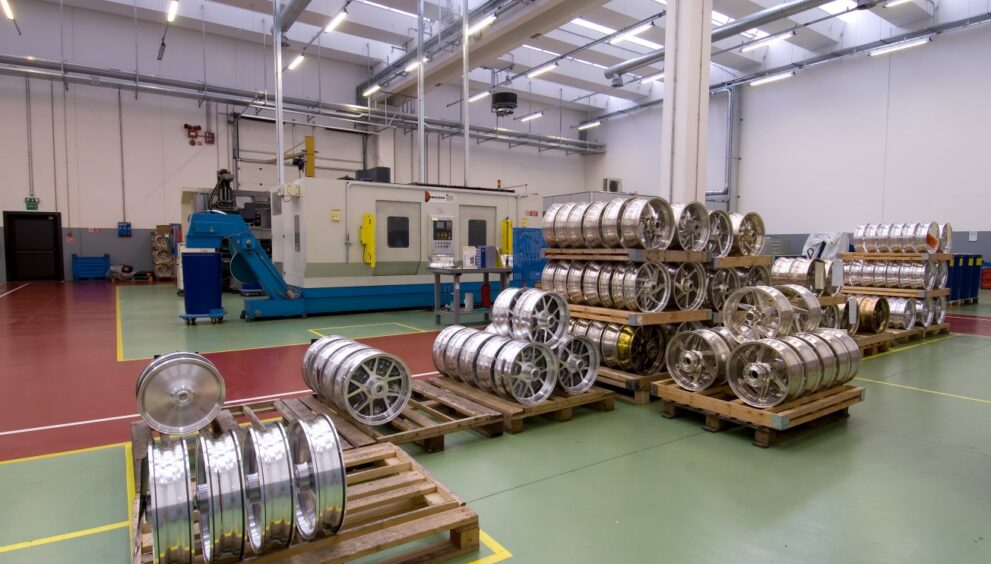
Come viene prodotto un cerchio in lega leggera
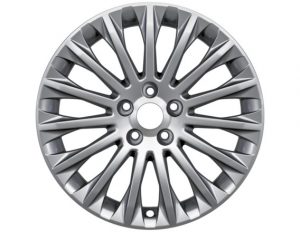
Un cerchione prodotto in lega leggera presenta vantaggi indiscussi dal punto di vista tecnico e pratico, ma richiede un processo produttivo più articolato e complesso. L’Italia è uno dei Paesi maggiormente avanzati nella ricerca e nella produzione dei cerchi in lega, annoverando diverse importanti aziende riconosciute in tutto il panorama europeo, che hanno diffuso brand altisonanti e oggi familiari a molti automobilisti.
Il processo produttivo si sviluppa secondo diverse fasi tra loro contigue, che devono compiersi con qualità e attenzione per poter ottenere un cerchio che possa rispettare gli elevati standard qualitativi e di sicurezza richiesti. Ciascun passo che compone la filiera di produzione non può prescindere da una scelta strategica di materiali selezionati all’origine e di lavorazioni da svolgersi in maniera precisa, per poter garantire la qualità e le attese dei clienti. Se per un cerchio in acciaio le aspettative non sono così pretenziose, un cerchio in lega deve saper fornire importanti riferimenti e soddisfare le maggiori esigenze.
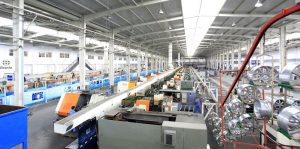
Il processo di produzione dei migliori cerchi in lega si compone di 8 fasi
- Scelta dei materiali: come dice il nome stesso, la materia prima che si rende necessaria per costruire un cerchione in lega leggera è appunto una lega di materiali e non un unico metallo. Per trovare il giusto mix è necessario far tesoro delle esperienze maturate nel tempo dall’azienda costruttrice, ma anche far leva sulle innovazioni tecnologiche prodotte dal comparto ricerca e sviluppo, sempre orientato alla scoperta di nuove opportunità. Il materiale principale è comunque l’alluminio, che si fonde insieme ad altri metalli in grado di conferire alla lega non solo leggerezza, ma anche proprietà tecniche specifiche, soprattutto meccaniche. La materia prima viene temprata per trattare adeguatamente la struttura e successivamente invecchiata per conferire maggior resistenza. Per cerchi in lega più performanti è possibile impiegare leghe di magnesio, più leggere fino al 35% rispetto all’alluminio. Queste, oltre a contribuire in maniera sensibile e decisa alla riduzione del peso, donano al prodotto grande resistenza agli urti, alle deformazioni e alle vibrazioni. Dopo aver scelto il materiale, si passa alla lavorazione vera e propria.
- La fusione in gravità: mediante l’azione della temperatura (circa 25-30 minuti in forno a oltre 700°C) e della pressione, l’alluminio, inizialmente in barre, viene fuso per esser colato nello stampo con differenti metodi. Una volta reso liquido entra in un miscelatore per la rimozione dell’idrogeno, importante per ridurre al massimo la porosità che si vedrebbe una volta tornato allo stato solido. A questo punto vengono aggiunti altri elementi, per fornire peculiarità differenti. L’introduzione di uno speciale agente chimico serve a questo punto per far venire a galla le impurità, le quali saranno poi estratte dalla miscela e tolte dal processo.
Lo stampo è composto solitamente da tre parti le quali, una volta riunite, costituiscono il luogo ove verrà colato l’alluminio fuso, che dopo circa 10 minuti si solidificherà prendendo la forma dello stampo stesso. Estratto, il cerchio viene immerso in acqua per il raffreddamento.
Alcune aziende utilizzano quello che viene definito un processo a bassa pressione, mentre altre impiegano la ”fusione di gravità”, a seconda di ciò che si desidera ottenere. Per garantire la massima resistenza ad un cerchio prodotto in bassa pressione è necessario sottoporre il prodotto grezzo ad un processo di trattamento termico.
- La forgiatura: questa è una fase chiave dell’intera produzione di un cerchio in lega che vuole essere di estrema qualità, poiché alla forgiatura spetta il compito di trasformare il progetto in oggetto, nel miglior modo possibile. Correttamente è opportuno precisare che tale fase è alternativa alla precedente e quindi non tutti i produttori la mettono in pratica, ma solamente chi vuole distinguersi offrendo al mercato un cerchio in lega di alta gamma. Questa operazione conferisce al prodotto una distribuzione uniforme delle sue caratteristiche fisiche, senza creare difformità tra zone che appaiono più resistenti di altre. Un buon cerchione deve essere forgiato per poter garantire resistenza, stabilità e sicurezza, a differenza della semplice fusione che genera discordanze tra la parte esterna e il nucleo della ruota. Per questo motivo, un cerchione realizzato mediante forgiatura avrà caratteristiche migliori (e costi più elevati) rispetto ad uno analogo che è stato semplicemente fuso per colata all’interno di uno stampo.
La forgia ha dunque il compito di incrementare le caratteristiche tecniche del prodotto, conferendogli una miglior risposta alle sollecitazioni, agli impatti e riducendo le probabilità di ovalizzazione. Inoltre se l’operazione viene svolta correttamente, un cerchio forgiato sarà tendenzialmente più leggero rispetto ad uno fuso, consentendo all’auto di esprimere meglio le proprie potenzialità dal punto di vista prestazionale e caricando di minor lavoro le sospensioni. A maggior ragione se si tratta di ruote che dovranno affrontare percorsi accidentati e strade sconnesse, il sistema sospensivo del veicolo sarà in grado di lavorare molto meglio, facendo percepire più comfort agli occupanti dell’abitacolo.
Tecnicamente la forgiatura riduce l’inerzia e quindi si verifica una perdita minore di potenza, migliorando il rendimento del motore, riducendo i consumi, migliorando la frenata e prolungando la vita utile degli organi meccanici interessati. Inoltre accelerazione e consumi trovano conferme migliorative. Per una moto, un cerchione realizzato mediante la forgiatura riesce a donare al motociclista una maggior stabilità e un miglior controllo, soprattutto nelle situazioni di emergenza durante cui è necessario frenare in maniera decisa e avere la maggior stabilità possibile del mezzo.
Tecnicamente, mentre la fase precedente prevede comunque una colata di alluminio fuso all’interno di uno stampo, nel caso della forgiatura si parte da un preformato ad alta pressione che viene lavorato ricavando, da un blocco pieno, la geometria del cerchione secondo il disegno del progetto. Il costo è più elevato perché si ha una qualità inarrivabile, ma anche molto scarto di materiale durante la produzione.
- La tecnologia: l’introduzione della tecnologia nella catena produttiva di un cerchio in lega è una componente determinante per la migliore riuscita possibile del pezzo. Non solo in fase di ricerca e sviluppo, ma anche in fase costruttiva e di test. Senza dubbio, infatti, la componente tecnologica si rivela fondamentale nei test del prodotto finito, ma lo è anche durante le diverse fasi di realizzazione. Forgiare un cerchio con un impianto innovativo, recente e dotato di grande intelligenza artificiale, consente di ottimizzare non solo la produzione dal punto di vista qualitativo, ma anche di ridurre i tempi di formazione del cerchio. Le migliori case produttrici attingono direttamente dai reparti racing, portando la tecnologia derivante dal mondo delle corse direttamente alla produzione di un cerchio stradale. A guadagnarne sono sicurezza e prestazioni, ma anche l’organizzazione e la pianificazione aziendale della casa produttrice. Applicando le più recenti innovazioni alle differenti fasi tipiche del processo produttivo, è possibile sopperire a eventuali mancanze, ottenendo, ad esempio, cerchi fusi con proprietà molto simili a quelle di un cerchio forgiato (ma mai uguali). Fin dalla progettazione del cerchio e dalla scelta dei materiali, la tecnologia ha grande incidenza sul risultato finale.
- Trattamenti termici: una volta che il cerchio è stato prodotto e assume una forma ormai quasi definitiva, è il momento di sottoporlo ai trattamenti termici di tempra e di invecchiamento. Il primo consiste nel riscaldamento fino a 600°C del prodotto al fine di stabilizzare le tensioni interne dei legami chimici molecolari della lega. Il secondo permette invece l’impiego strutturale del materiale e può essere realizzato in modo naturale per i cerchi in magnesio, oppure artificiale per un cerchio in alluminio. Complessivamente il ciclo di trattamenti termici dura circa 10-15 ore per la fase di tempra e circa 8-9 per quella relativa all’invecchiamento.
- Altre lavorazioni: una volta fuso o forgiato, il cerchio in lega deve essere in qualche modo ”rifinito” e completato. Il foro centrale viene realizzato con una lavorazione di tornio, mentre la fresatura interessa la rifinitura delle razze. Inoltre, i cerchi in lega più pregiati, si avvalgono anche di una fase manuale di sbavatura che avviene in maniera precisa e puntuale, prima di esser sottoposti alla cosiddetta pallinatura, trattamento superficiale atto a migliorare le proprietà superficiali del pezzo.
- Test: prima dell’ultima fase e dopo le lavorazioni di sbavatura, è tempo di collaudi per il cerchio.
Dapprima viene immerso in acqua per qualche secondo prima che venga addizionata con aria. Questa fase serve per verificare che il cerchione non abbia forature o cricche, le quali, se dovessero apparire, comporterebbero la difettosità del pezzo e il suo conseguente scarto.
Un ulteriore test viene svolto applicando il cerchio ad un apposito macchinario in grado di simulare diversi chilometri di marcia per valutare usura, prestazioni e grado di ovalizzazione. Se i parametri riscontrati rispondono alle attese, il cerchio è pronto per la fase finale di finitura.
- La finitura: come accennato, il cerchio in lega deve anche avere un aspetto estetico di notevole impatto, in grado di stupire. Alcuni presentano un aspetto anodizzato per proteggere dalla corrosione e donare all’esterno un aspetto più accattivante e piacevole. Sopra ci va però la finitura e quindi la verniciatura. Più strati di speciali polveri di materiale epossidico vengono sovrapposti e fissati a caldo prima di verniciare con la tinta desiderata. Per finire viene applicato il velo di trasparente che ha lo scopo di vivacizzare il colore e proteggere la superficie da graffi e agenti atmosferici.